SICK is a global leader in intelligent sensing solutions for warehousing and logistics automation. SICK sensors form the basis for automating material flows and optimising sorting and warehousing processes all over the world.
SICK solutions reflect the company’s extensive expertise and experience in control, identification, monitoring and measurement processes, developed in close partnership with blue-chip retail, manufacturing and logistics operators across many industry sectors. From machine vision to RFID; barcode readers to integrated company-wide systems; laser scanners to light curtains, SICK solutions represent the latest in auto-ident, measurement and personnel safety, backed by a commitment to innovation and R&D which keeps all its product ranges at the cutting edge of technology.
In factories, warehouses, distribution centres and airports all over the world, SICK sensors can be found performing the functions that smooth operations day by day, whether detecting the presence of goods, dimensioning parcels, positioning high-bay cranes or protecting workers entering dangerous areas. From goods inwards all the way through to final shipping, SICK sensors offer integrated solutions based on robust and reliable reading, capture and communication of data and images that can be managed by central warehousing and distribution control systems.
SICK is celebrating its 40th Anniversary in the UK, so Warehouse and Logistics News spoke to Gary Young, UK Segment Manager for Logistics Automation to discover how the company is responding to the auto-ident and automation challenges for operators in today’s fast-moving materials handling and distribution environments.
Warehouse & Logistics News – Gary, as SICK’s UK Segment Manager for Logistics Automation what does your role involve?
My role provides a focus for all sales support to the materials handling, warehousing and logistics sector. With such significant expertise and specialist technologies in this sector, SICK understands the importance of having a dedicated sales team with in-depth knowledge of customers’ operating activities, backed by the knowledge of auto-ident and safety product specialists.
WLN – Where is your UK HQ?
SICK’s offices in St Albans are the headquarters for its UK sales and support operations. Our 24/7 support, spares and service operations are organised from this centre, too.
WLN – SICK is surprising name for a company – where does it come from and what is the company’s history?
Yes, SICK is certainly a very memorable name that even earned us a spot on “Have I Got News for You” recently! SICK is actually the name of the company’s founder, Dr Erwin Sick, who started the company in Germany more than 60 years ago. SICK has since become a global company, but still remains a family-owned business today. Most of our sensors are manufactured at SICK’s original facility in Waldkirch in Southern Germany.
WLN – In the UK SICK is celebrating its 40th birthday. What changes has the company seen in sensor technology over that time?
40 years ago, simple optical sensors were as big as milk bottles; now it’s possible to get amazing performance out of a device the size of your little fingernail. Just compare the supermarket of 40 years ago with today and it’s clear that technological advances have been behind a huge explosion in the number of products shipped across continents and brought to our doorsteps in the sophisticated logistics operations we take for granted. SICK technology offers in-built Sensor Intelligence that enables high-speed, flexible, traceable and safe automation in production, warehousing and logistics.
WLN – Who are SICK’s customers in the UK for logistics automation?
SICK solutions are currently being used by major UK airports for baggage handling, by the best-known names in parcel handling and by the logistics operations of many major retail and grocery chains. They are widely used in food and beverage manufacture and distribution by leading international brands. Of course, not all our customers are household names, but we believe our close understanding of the industry means we can recommend the right solutions in each case – as well as innovating new technologies to meet our customers’ needs.
WLN – What sets SICK apart as a supplier of sensing solutions for logistics automation?
Because SICK has such a broad range of products, there’s no need to make ‘one size fit all’ as some of our competitors have to do. We have no allegiances to one particular technology so we can offer the best solution for each application, be it a machine vision camera, a laser sensor, a barcode reader or RFID system.
WLN – How do SICK products address the key challenges faced by warehouse and logistics operators?
Undoubtedly, the first challenge for our customers begins with inbound goods and overcoming the frustrations of poorly printed barcodes, mislabelled products or damaged boxes. SICK has systems that can help address all of these problems and automate the vendor compliance process to reinforce Service Level Agreements and keep the lines running.
WLN – Can you give some examples?
Yes, I can. The SICK ICR890 is a camera system that reads 1D and 2D barcodes in high-performance sortation systems, reading up to 6 sides of a package if necessary. The image captured can be also be read using OCR while the package remains on the sorter, avoiding the need for manual handling where the barcode is unreadable. Another benefit to the customer is NORCA which can identify the reason for a barcode being unread. Trends can be detected and reported automatically therefore ensuring the labels are changed before they become an issue.
To maximize throughput in high-speed receiving areas, SICK systems can be used to automatically identify, weigh and dimension goods. The VMS (Volume Measurement System) can verify the volume of a package against a supplier’s inventory and DWS (Dimension Weighing Scanning) systems can also be integrated to capture weight data, too.
WLN – Operators are facing tough economic times. Do solutions from SICK bring a return on investment?
Our customers are looking for ways to maximise their uptime, optimise their storage space and reduce their energy consumption. All SICK solutions are focused on getting the best operating availability with quick and easy commissioning when sensors need to be replaced.
WLN – How do SICK products achieve cost savings in materials handling and distribution?
There are so many examples. Barcode readers such as the SICK CLV6XX series, for instance, can achieve near-perfect read rates of tote labels with extremely fast throughput speeds, yet installation and commissioning is simply ‘plug and play’.
The SICK MCL is a vision-based system for automated, on-demand maintenance inspections of sorters. Easily installed onto an existing sorter frame it works stand-alone, without interfering with the sorter’s control system and without stopping normal sorting activity. As a result, higher availability of the sorter is achieved, with lower total maintenance and power consumption costs.
Using a vision camera such as the SICK IVC2D to inspect for empty totes is another example of a cost saving application by preventing the possibility of ‘shipping air’ and thus incurring unnecessary freight costs and even potential fines from customers.
With SICK VMS, warehouse use can be optimised to make the most of available storage space by measuring the volume of each package and calculating the optimum position for it to be placed by an automated crane. Volume measurement can also be used to ensure bowed or damaged boxes are rejected before they cause costly downtime.
WLN – Looking back, what were some of the earliest technologies developed by SICK?
Sixty years ago, in post-war Germany, Erwin Sick developed the first single light source light curtain, using a rotating mirror to project the light beams. At the time, this was quite revolutionary; losing hands and fingers was commonplace. Now we rightly expect the highest levels of employee safety and protection and SICK has a well-established reputation as a leader in the field of safety.
SICK photoelectric safety switches, laser scanners and light curtains protect people from entering unsafe areas and prevent AGVs and forklifts from colliding or causing danger to personnel. SICK’s outdoor scanners also protect the security of the buildings themselves.
WLN – What is the latest safety technology available from SICK?
With the launch of the SICK deTec4 Core we believe we have achieved the next-generation of safety light curtain, setting new performance standards in efficiency, installation and reliability. The SICK deTec4 Core sets a new benchmark for single-sided access protection.
As well as meeting the latest EN standards, the deTec4 Core has no blind zones, offering optimum positioning and protection against unsafe access whilst enabling ongoing efficient operation. Through the space saving, robust design safety distances can be minimised to achieve best-possible machine integration as well as higher operator productivity.
WLN – Looking to the future, what industry trends will drive further technology innovation?
There’s no doubt that our customers are demanding greater speed and flexibility in operation, often with a greater range of goods. They want to be able to guarantee as near perfect as possible read rates even at high speeds. They want to be able to maximise the use of their storage space and the availability of their automated processes.
However, more than anything, it’s the requirement for tracking and tracing goods that is at the forefront of technological development. In retail distribution, for example, customer engagement is paramount and the expectation is that customers can track the progress of their delivery at every stage.
WLN – Can you tell us about the new SICK SVP system?
The SICK Visualisation Platform (SVP) is an exciting development that can help logistics businesses open a ‘visual’ window on a wealth of information gathered from SICK data collection devices, including laser and barcode scanners, camera systems, RFID and dimensioning and weighing systems.
For a long time, logistics businesses have been frustrated that all the information collected during goods handling cannot be used to monitor performance without laborious translation of data across platforms. The new SICK SVP600 ends the wait, bringing the best in Sensor Intelligence and Automated Data Collection (ADC) technologies together in a powerful data search and retrieval system that can deliver a wealth of information at your fingertips wherever you are in an organisation.
SVP offers unprecedented real-time access to data, images and video across logistics and materials handling operations. The system manages auto-identification data collection, storage and retrieval across an enterprise with tools to track and evaluate operational performance.
The Sick SVP is a dynamic database that can be used for real-time tracking of goods across a complete logistics system providing network visibility to data and images and providing users with current and archived information to enable analysis and reports.
The new SICK SVP600 provides visibility to processes where SICK devices are used and helps users evaluate the key variables that affect material flow through their distribution centres. Real-time feedback about system activity and performance is accessed from the SICK SVP Dashboard displaying everything from percentage barcode reads to image retrieval that can visually identify parcels or verify the condition of packages.
WLN – Does SICK sensing technology offer solutions for secure shipping?
Yes, we do. The new SICK LAC (Logistics Access Control) system was launched at this year’s IMHX Show. It provides a ‘virtual lock’ on access to designated secure areas for overseas goods transportation.
International anti-terrorism measures are placing increased demands on logistics operators to demonstrate to customers they have secure shipping arrangements in place that can guarantee to avoid any costly hold-ups by customs authorities.
The SICK LAC combines non-contact laser measurement sensing with long-range RFID technology and integrated software in one complete, ready-to-use system. The result is a unique customs-compliant access control system solution which provides a ‘virtual lock’ to ensure secure access of people and goods into designated secure areas and, in particular, can support operators with ‘Known Shipper’ status for air freight to the US.
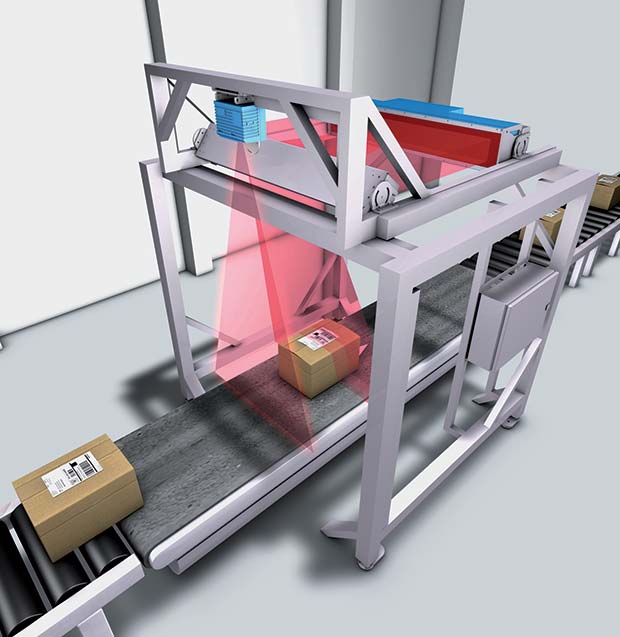
WLN – How can potential customers find out more about your company and your solutions?
They can phone the logistics automation team on 01727 831121; email me [email protected] or visit our website www.sick.co.uk to request a subscription to our customer magazine Sick Insight, or download our Warehousing and Distribution Industry Guide.
They can also follow us on Twitter page @SICK_UK and Facebook page – www.facebook.com/SICKUKLtd. I would also recommend the videos on the SICK YouTube channel – www.youtube.com/user/SICKSensors.